Welcome to our environmentally-themed Q&A blog featuring our Quality Manager, Shane Cutting. At Fireco, we’re dedicated to ensuring a sustainable future. We’ve made significant progress in reducing our carbon footprint, implementing recycling programs, and embracing renewable energy. In this blog, Shane shares insights into our green initiatives, answers questions on sustainability, and provides tips on how businesses can contribute to a healthier environment.
Hi Shane, thanks for joining us. Can you tell us a bit about your role at Fireco?
My official title is Quality Manager, which means I’m responsible for all things quality and environmentally-related. I’ve worked at Fireco for over 12 years, within various departments of the company, so I know the inner workings very well by now.
What is it about your role that you particularly enjoy?
To be honest, coming into Quality wasn’t necessarily something I thought I’d enjoy! It just so happened that a series of events occurred, and, long story short, I proposed to my manager that it seemed we needed a singular go-to person to resolve all quality-related aspects of the business. She went away, thought about it, and created the job for me the very next day.
Overall, it’s been quite a steep learning curve, but I enjoy the challenge. I’ve had to work hard to understand the various accreditation obligations. Since I’ve started, we’ve passed every audit smoothly, and I’ve even overseen a recent ISO9001 recertification process, which was daunting, but we passed it successfully.
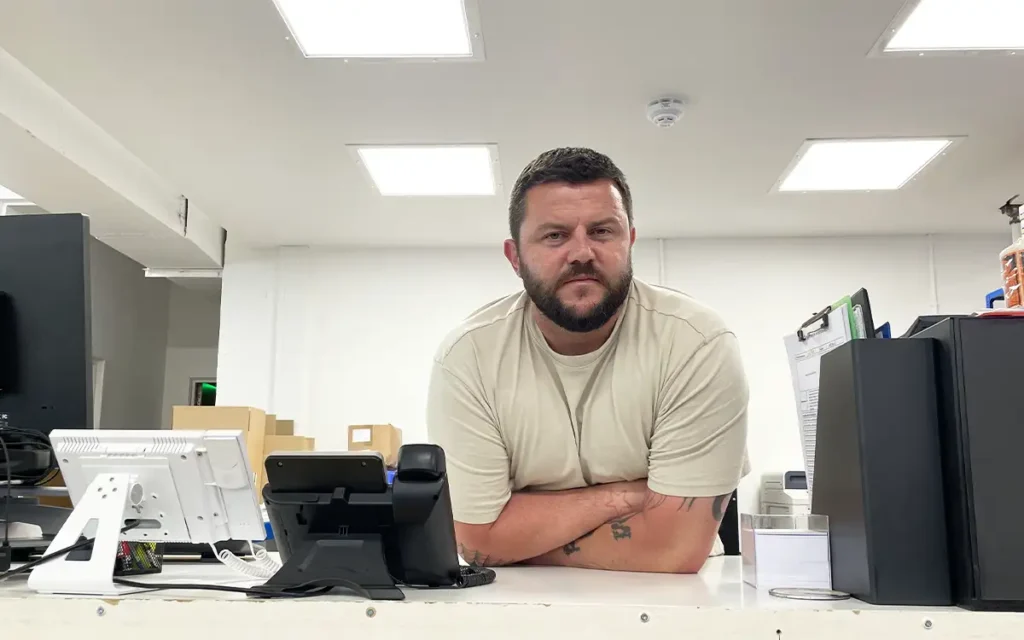
Looking ahead: Shane Cutting, Fireco’s Quality Manager
Why is it important for businesses and manufacturers to focus on their environmental impact?
I think environmental improvements are a fundamental part of every organisation these days, and I’m proud of how we take them seriously here at Fireco. We’re very aware of our environmental impact, and improving our performance is a core aspect of our ethos. It’s also a huge area of focus for our parent company, Lagercrantz. It was agreed at the Paris Agreement in 2015 that countries all work together to lower our emissions by 2030, which shows that everyone’s taking the climate crisis more seriously. We’re just happy to do our bit as a small cog in the machine.
What changes have been implemented so far?
There have been many. The first stepping stone was that we achieved ISO 14001 certification in August last year. From start to finish, it’s been a long process. It takes roughly a year and a half, and it shows that we’re aware of our environmental obligations and the legislation relating to our business. This requires us, through an Environmental Management System (EMS), to monitor and manage our environmental impact and performance and actively work to improve them through clear goals and strategies.
So one of the things we’ve done is to have an array of 77 solar panels on the roof, which has drastically reduced the amount of electricity we’ve had to purchase from the grid. Any excess energy is sold back to the provider. The solar panels feed EV charging points at the side of the building to facilitate staff members with EVs.
We’ve also implemented a fully recyclable plastic dispatch, so everything that would’ve once been single-use, like pallet wrap, document envelopes, jiffy bags, etc., has been replaced with recyclable, compostable alternatives, such as ones made from sugarcane.
Where possible, we have hybrid vehicles for staff, but unfortunately, due to the nature of the business and the long distances that sometimes need to be travelled, we don’t use EVs for our Field Service Engineers. When the technology and range of the vehicles improve, we will definitely revisit this. However, we do use a courier that has a fleet of EVs for shorter distances, and uses biofuel in their long-distance trucks.
We’ve also adopted our parent company’s key environmental target of reducing all of our emissions by at least 50% by 2030. As part of this, we produce sustainability reports quarterly that monitor our environmental performance.
We recently removed a lot of optional plastic components from the Dorgard accessory boxes, as it’s believed that a lot of them are not used and thrown away.
Another big thing is that all of our cardboard comes from a company that manufactures it using material that is between 79-100% fully recycled.
You were in the process of a task where you tracked the environmental impact of each and every part of a product on its journey, e.g. whether it was shipped or flown. Can you tell us about this?
This is part of a bigger project called ‘The Life Cycle Analysis’, and it’s where we go through the process of examining a product’s life span, and understanding the different stages it goes through. This information can then be used to make better decisions in the future about sourcing components, where we can save money and reduce our environmental impact. We’re still immersed in the project because of the level of detail required. For instance, you have to weigh every single product, list its components, where it comes from, where it’s going, its manufacturing process. All these factors combine to provide an overall emissions figure, and then we can work towards reducing that.
What other changes and goals are on the horizon?
The big one is to meet Lagercrantz’s target of reducing our overall emissions to 50% by 2030, which I know we’re fully on our way to achieving. Currently we’ve cut our emissions CO²e (ton) by 12.27% from our base year of reporting, 2021-2022.
Can you name some useful resources to help people inspired by this blog to make similar changes?
In all honesty, one of the main things we did was just read everything that’s out there. Go through the ISO 14001 accreditation requirements and understand what it’s asking of you. The gov.uk website is fantastic, there’s so much stuff on there relating to all the legislation that you need to adhere to. Another really good resource that we use is the UN’s 17 sustainability goals that they’ve highlighted. Our parent company has adopted these and put them in their sustainability reports, so it follows that we’ve taken the same approach.
Why was gaining the ISO 14001 accreditation so important?
Like 9001, which is the quality management system accreditation, this gives people confidence that you’re putting your money where your mouth is, environmentally. With the 9001, having that certification means that we can sell to the larger organisations like the Screwfixes and Toolstations of the world. Having the 14001 accreditation gives people confidence that we’re making efforts to improve our environmental performance.
We’re actually one of the first companies within our parent company’s group to achieve this accreditation, and as a result we’ve been leading the way in helping some of their other companies gain this accreditation by sharing our knowledge, which has been great.
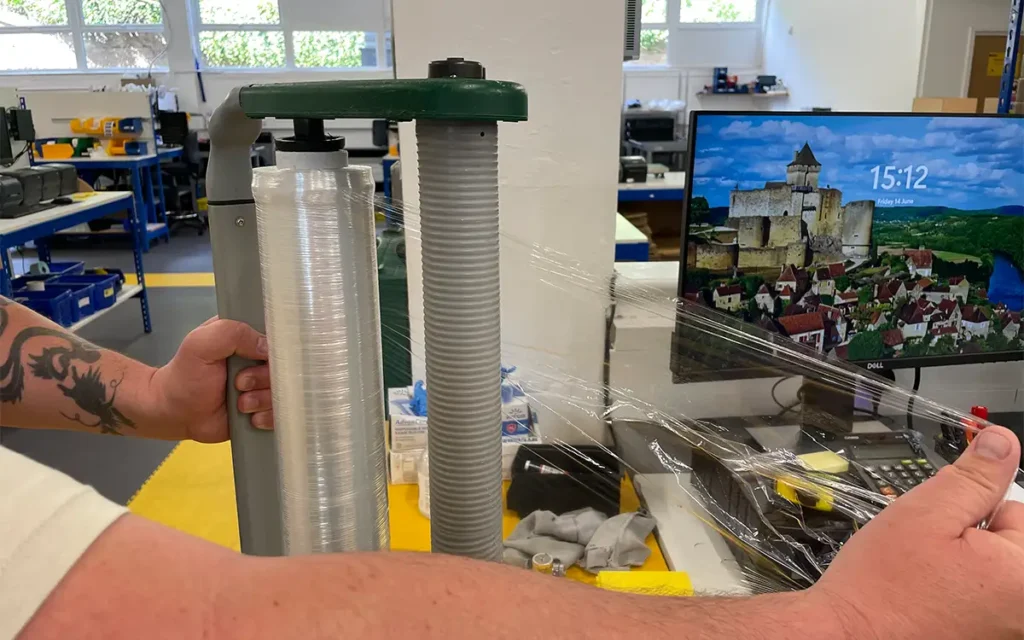
Clingfilm wrap made of sugarcane
Can you tell us a bit more about obtaining that accreditation?
One of the key things we had to do was draw up a legal register with pretty much everything that you could possibly think of associated with our manufacturing business. Another big one is the Aspects and Impacts Register, which contains all of the various environmental aspects (risks) that can impact your business. This includes everything from facilities management – the use of cleaning chemicals, for example, to the material and resource consumption of the business. It’s an important tool as it’s used to identify the aspects, rate them and then implement control measures to negate their environmental impact.
Thank you, Shane. Finally, which changes are you personally proud of and excited about?
It’s the fact that we’re making physical changes and actively working towards our environmental goals, and we’ve done it all from scratch. Two years ago, none of this existed. It’s been a huge learning curve and everyone involved has pulled together to make it happen. I couldn’t be prouder, personally.
0 Comments